Lean management: voorkom het jojo effect
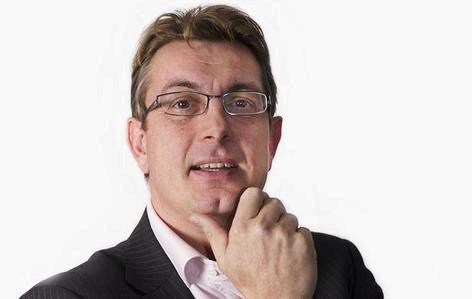
Wanneer de aandacht die het onderwerp heeft gekregen echter vermindert en de resultaten niet worden geborgd in de staande organisatie, wordt het schijnbare succes grotendeels teniet gedaan. Totdat het onderwerp weer actueel wordt en het onderwerp opnieuw wordt opgepakt. Dit zogenaamde jojo effect staat haaks op de filosofie van Lean Management: continue verbeteren als onderdeel van het werk.
De weg naar continue verbeteren is geen kwestie van het opleiden van een paar Belts, het uitvoeren van een paar projecten en hopen dat dit zich als een olievlek over de rest van de organisatie verspreid. Integendeel: de weg naar continue verbeteren is een bewuste keuze van een organisatie. De keuze om zich te ontwikkelen tot een flexibele en zelfkritische zorginstelling die in staat is de zich snel voltrekkende veranderingen in de maatschappij van nu te kunnen bijbenen.
Om teleurstelling te voorkomen is het goed dat organisaties weten dat de weg naar continue verbeteren gefaseerd verloopt. Dat men dus niet moet stoppen wanneer de eerste successen zijn weg geëbd, maar dat de organisatie bewust de stap naar de volgende fase maakt. Onderstaand figuur geeft een beeld van deze gefaseerde reis.
Uit bovenstaande figuur is af te leiden dat de projectmatige opzet verandert in een continue proces optimalisatie. Dat wil zeggen dat verbeteronderwerpen niet meer worden opgepakt vanuit een tijdelijke projectorganisatie met de daaraan gepaard gaande belasting. Hierdoor worden verbeteringen niet meer ervaren als projecten die bovenop het dagelijks werk komen, maar dat verbeteren onderdeel is van het dagelijks werk. De parabel van de houthakker die zijn bijl nooit slijpt omdat hij daarvoor geen tijd heeft is dan ook verleden tijd. In plaats van extra energie verspillen door te hakken met een botte bijl, wordt de bijl elke dag even kort geslepen. Zo verworden knelpunten niet tot onoplosbare problemen, ze worden in de kiem gesmoord.
Hieronder staan enkele tips die kunnen helpen om continu verbeteren in de praktijk te brengen:
– Verbeteringen vinden plaats op de werkvloer (gemba op zijn Japans) Dat betekent dat ook de managers de meeste van hun tijd op de werkvloer moeten doorbrengen (go gemba) en hun ogen de kost moeten geven. De werkvloer kan de echte fabrieksvloer zijn maar ook een klantgesprek door een verkoper of een bed. Overal waar direct waarde wordt toegevoegd voor de klant. En hoe vaak wordt waarde toegevoegd op een (hoofd)kantoor?
– Plaats elke verbetering in een breder perspectief door de lange termijn planning helder te hebben. Bij Toyota moet elk van de verbetervoorstellen bijdragen aan een van vier doelstellingen van het bedrijf (100% toegevoegde waarde, one piece flow, medewerkers veiligheid of nul fouten). Deze doelstellingen worden voor elke proces vertaald in doelstellingen die binnen 3 maanden te realiseren zijn. Zo maak je de invoeringstermijn overzichtelijk en realistisch
– Haal obstakels die de doelstelling over 3 maanden in de weg staan één voor één weg. Zo maak je de te nemen stappen klein, weinig arbeidsintensief en je ziet het effect van de verbetering. Zijn obstakels niet weg te halen middels een kaizen aanpak? Dan kan een LSS project wellicht uitkomst bieden.
– Voer een strakke discipline op continu verbeteren. Zorg voor een open sfeer waarin verbeteringen mogen worden aangedragen en niet de aandrager wordt benadeeld (met andere woorden ‘blaim-the-process’, not the person). Maar zeg ook tegen medewerkers dat elke mogelijke obstakels “verplicht” moet worden gemeld. Met visueel management (verbeterborden) kunnen deze voorstellen worden geprioriteerd en worden de belangrijkste opgepakt.
Voorbeelden van de toepassing van continue verbeteren in de zorg zijn:
– Het bieden van waarde toevoegende diensten – juist in deze tijd waarin de financiering van de zorgproducten op de schop gaat, is innovatie en participatie bovenop de bestaande verpleging en verzorging een must.
– Capaciteitsplanning is nog zo’n hot item – niet alleen de analyse van de ZZP mix versus de medewerkers mix moet gedaan worden maar juist de manier waarop de planning tot stand komt: hoe gaan we om met niet-werkdagen van parttimers, vraaggericht roosteren, vakantiespreiding, uitwisseling tussen locaties.
– Het terugdringen van incidenten, door een grondige analyse op oorzaken van incidenten, kan kostenbesparend werken en is positief voor het imago.
– Iedereen ziet dagelijks verspillingen: het elimineren van bijvoorbeeld het zoeken naar materialen, wachten op een collega of cliënt, dingen op meerdere plekken opschrijven, voorraad houden van materialen en geneesmiddelen op diverse plekken kan aanzienlijke besparingen opleveren.
De zorginstelling die zich op deze manier weet te ontwikkelen zal merken dat de resultaten goed zijn en dat niet alleen de cliënten maar ook de medewerkers meer tevreden zijn. Uit onderzoek blijkt dat medewerkers die actief betrokken zijn bij de ontwikkeling van de organisatie aangeven het gevoel te hebben ertoe te doen. Dat gevoel is een belangrijke voorwaarde om goed te scoren op medewerker tevredenheid. De grondlegger van Lean Management, Taiichi Ohno, heeft gezegd: ’De stijl van Toyota is niet om resultaten te boeken door medewerkers harder te laten werken, maar om optimaal gebruik te maken van hun creativiteit. Medewerkers komen niet naar Toyota om te ‘werken’ maar om te ‘denken.’ Het is het meest waardevol voor elk bedrijf: de creativiteit van de medewerkers om de kennis die zij van de bedrijfsprocessen hebben zodanig in te zetten dat er nog meer waarde wordt toegevoegd aan de producten of dienstverlening. De potentie hiervan wordt in verreweg de meeste organisaties slechts voor een fractie benut.
Het toepassen van Lean Six Sigma met als doel het opbouwen van een zich continue verbeterende organisatie vraagt dus om een bewuste keuze van een organisatie. Al is de keuze niet zo vrijblijvend als het lijkt. In de tijd van Ford voltrokken veranderingen zich relatief langzaam. Heden ten dage is het tempo zo hoog dat het noodzakelijk is om snel te kunnen reageren. Dat lukt alleen de organisaties met een hoog proces bewustzijn waarbij veranderen ten goede onderdeel is van het dagelijks werk.