Leveranciers laten meedenken leidt tot nieuwe ideeën en besparingen
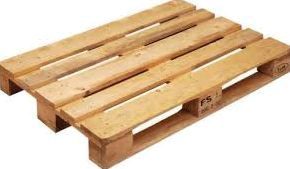
Door Steven Bakker19 jaar pallets van dezelfde leverancierTrespa zocht een manier om het inkoopproces te verbeteren en kosten te besparen. Het internationale bedrijf was zelf een expert in het inkopen van grondstoffen, maar zocht verder naar manieren om de productiviteit te verbeteren. Eén van de belangrijke onderdelen van de productprijs was het gebruik van custom pallets.De fabrikant maakte gebruik van deze pallets om materialen te vervoeren. De huidige leverancier leverde al 19 jaar aan het bedrijf. De houten pallets werden in Antwerpen gemaakt en ongeveer 80 kilometer verderop met een vrachtwagen afgeleverd. De gemonteerde pallets werden op locatie opgeslagen en daarna, geladen, over heel de wereld verscheept. Onmogelijk om te besparen op pallet-prijsDe prijsconcurrentie voor pallets is gigantisch. Vanwege het grote aanbod is het bijna onmogelijk om pallets als producent goedkoper aan te bieden. Switchen tussen leveranciers zou dus weinig opleveren. De fabrikant moest breken met de oude manier van werken en vroeg Emeritor om een nieuwe methode te zoeken om de kosten te verminderen.Leveranciers kregen inzicht in het productieprocesDe fabrikant besloot de expertise van de leverancier te gebruiken. Hij nodigde drie palletleveranciers uit, waaronder de huidige. Zij mochten iedereen op de locatie bezoeken en kregen de mogelijkheid om vragen te stellen aan het personeel. De leveranciers kregen op die manier een indruk van het hele productieproces. Vervolgens werd hen gevraagd om hun bevindingen te presenteren aan de directie. Dit leidde tot drie zeer verschillende presentaties, waarin de leveranciers toelichtten hoe zij de pallets in het productieproces zouden integreren. Nieuwe ideeën en 25% besparingDe zittende leverancier was tevreden met de situatie. Beter kon het niet volgens hem. De andere leveranciers gaven heldere inzichten en kwamen met interessante nieuwe ideeën. De leverancier die na het traject een overeenkomst tekende, kwam met het idee om de pallets on-site te monteren. Het aantal transporten verminderde. Een vrachtwagen kan veel meer losse planken vervoeren, dan complete pallets. Dit leverde niet alleen een financiële besparing op, maar ook een CO2-reductie van 60 ton per jaar. De leverancier zette een geautomatiseerde productielijn neer, waarmee heel snel verschillende typen pallets gemaakt konden worden. De totale kosten van de pallets, waaronder het transport, monteren en opslaan van pallets werden met 25% verminderd.Samenwerking CFO en COOIn de besluitvorming hebben de CFO en de COO van Trespa nauw samengewerkt, vooral om de risico’s goed in kaart te brengen. Voor deze innovatieve besparing moest de CFO breken met tradities en ingesleten processen. Daarnaast moest de leverancier de kans krijgen om zijn verdiensten te maximaliseren, zonder dat die afgeroomd werd door de klant. In de samenwerking was deze “gunfactor” een belangrijk uitgangspunt. Inmiddels twee jaar verder zijn de verwachtingen rond de besparingen meer dan waargemaakt en is de samenwerking nog steeds succesvol. Steven Bakker werkt bij Emeritor en beschrijft in zijn blog voor CFO.nl business cases waarin bedrijven door creatief te zijn tot een goed resultaat te komen.